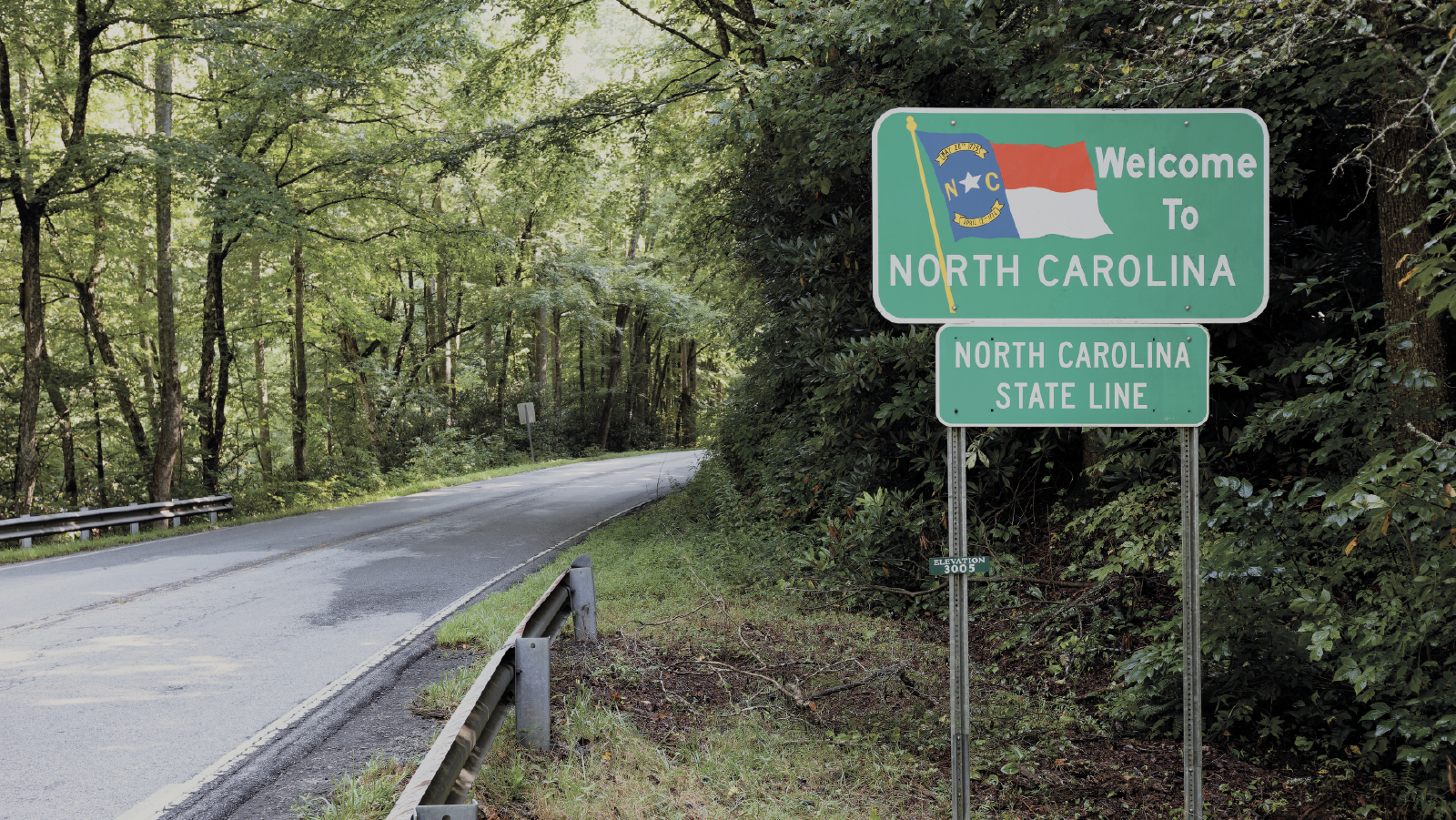
Dennis Nobelius: Action speaks louder than words
My reflections from the past month
To succeed, we need to be big, and to be a big global partner we need to be neutral and work with all brands, industry verticals, company sizes, and supply chain partners. We strive to be a strong collaborator that cheers for our peers, the other textile-to-textile suppliers. Together we can develop standards and categories to drive the change needed.
Bottle-to-fibers (rPET) i.e. today’s recycled alternative, is soon out of fashion for textiles (apologies for the pun). The Coca Colas of the world are already frowning that their EPR schemes are going into another industry, EU legislation with Green Claims initiative is about to abolish rPET as a sustainable circular solution, and on top of that – prices for rPET will increase. Circular polyester produced by textile-to-textile recycling is the future.
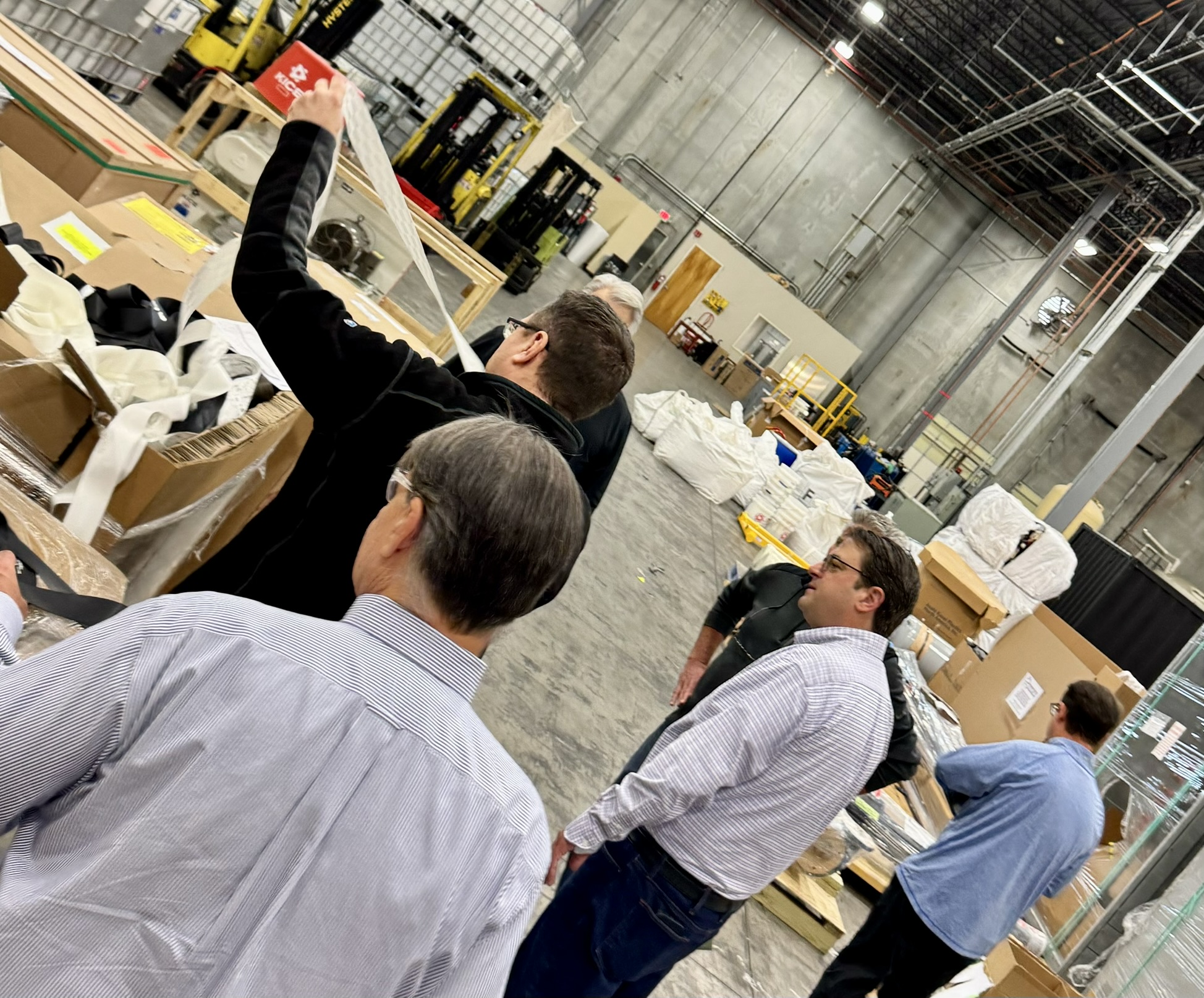
We need to be bold and act now
Brands may choose to adopt a ‘wait and see’ tactic, looking at us and others and say: “I wonder if this will work this time”. Or,preferably, they say: “Great, here are partners aiming for scale, let’s support this to bring us as an entire industry forward”. We really need to work together to be successful, from commitment to execution. Why do we need to be successful? Because our industry and planet urgently need it.
“Climate crunch time is here”, said Inger Andersen, the Executive Director of UN Environment Programme (UNEP) during the launch of The Emissions Gap Report at COP16 biodiversity conference two weeks ago. The report highlights the critical need to drastically reduce emissions by 42% by 2030 and 57% by 2035, without which the world risks a 3.1°C temperature rise. These urgent numbers underscore the need for solutions to scale and spur our ambitions to increase speed. Which is exactly what we’re here to do.
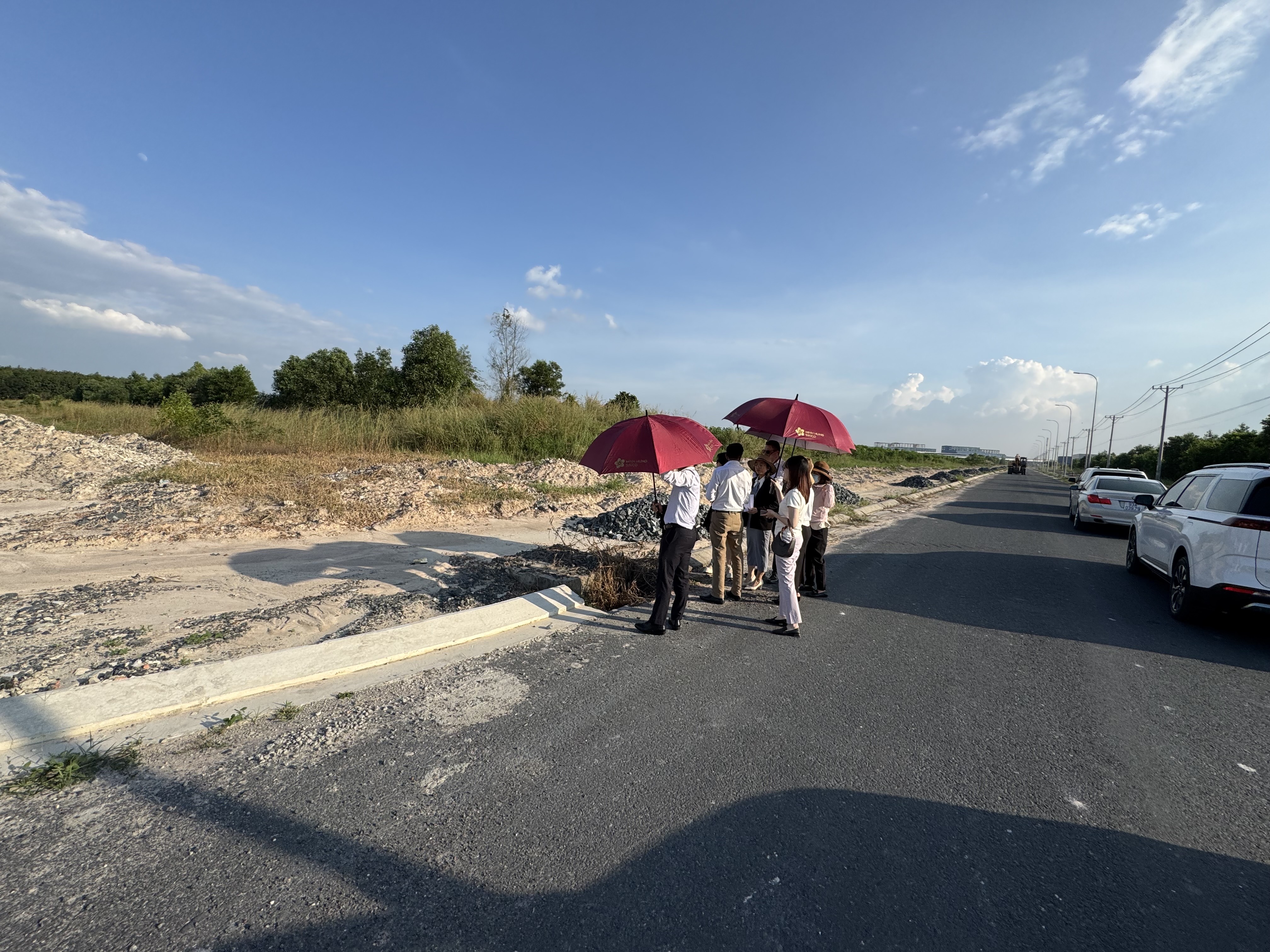
Syre’s Blueprint plant is here and sets the foundation for our future
Last week we were finally able to communicate that we are teaming up with Selenis, a global specialty polymer company, to open our Blueprint recycling plant in Cedar Creek, North Carolina. A truly important milestone for us! We already had the equipment, machinery and engineering drawings for a Blueprint plant with a yearly capacity of 10 000 metric tons of circular polyester. We had everything we needed for pre-processing all the way up our (key IP and trade secret element) of depolymerization. But we lacked polymerization units.We could have performed toll manufacturing i.e. sending our end stage BHET tosomeone else to polymerize. But this would mean that we would lose out on thecontinuous flow and learnings thereto. Speed and continuous iterations are key. Hence, when we discovered that Selenis, led by Duarte Gils, had a Brownfield plant in an industrial park in the same state as our R&D Pilot Line this seemed like a match made in heaven.
The Blueprint plant of Cedar Creek will provide us with the best technology proof point available. Taking all explorations and innovations that we test and develop in our R&D Pilot Line in Mebane, NC, into continuous flow and with standardized processes. The learnings from our Blueprint plant will lay the foundation for first our gigascale plant-to-be (150KMT – 250K MT capacity) in Vietnam.
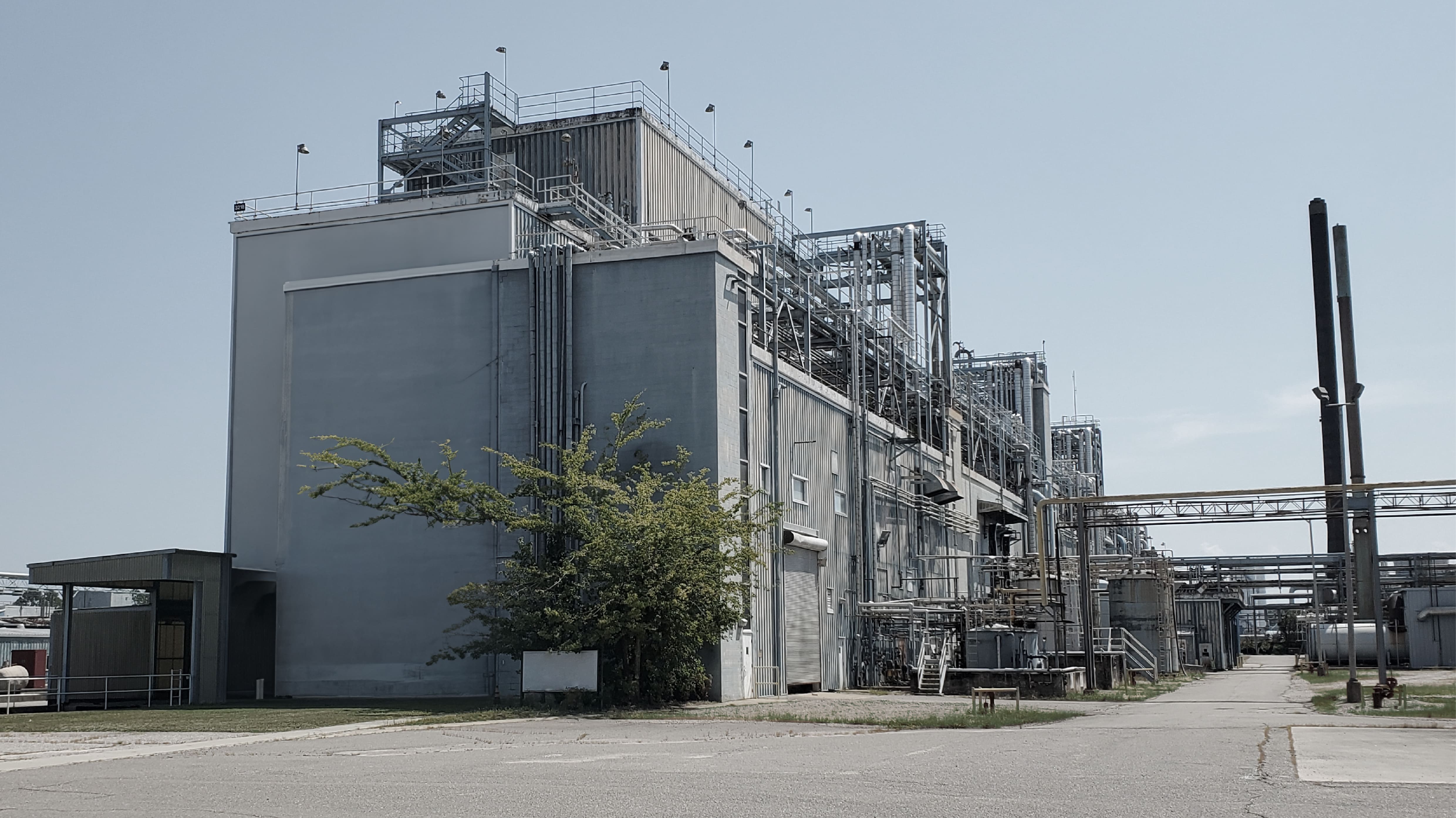
Innovation is happening—R&D lab and pilot line in Mebane, North Carolina
We have not touched too much about this previously, but our R&D Pilot Line is now moving from Garner to Mebane, North Carolina, where we will establish an office, an R&D lab and a pilot line including feedstock storage possibilities. In parallel, we work intensely with getting samples out the door showcasing our capabilities. Although there was a fire in our polymerization partner’s equipment in Germany and we ran into contamination from our Garner pilot line warehouse during a manual non-relevant step, we are still preparing for the move to Mebane, expected to be completed in the coming month.
Commercial volumes by end of 2025
Back to the Blueprint plant, what does this mean for us timing-wise with having an integrated Brownfield (= also reuse, better than building new) plant? Well, the team is now working to finalize all operational items – order flows, feedstock storage, pre-processing unit placement (28 tons of dynamic load requires a stable foundation), and making our equipment and processes fit into an existing compact facility. We are getting ready for cold-commissioning Q1/Q2 meaning commercial volumes by end of 2025. Not bad for a newly launched scale-up, right? In parallel we work with the prerequisites for the gigascale plant in Vietnam. For that step, we will also finalize our Series B, but now I’m getting a head of myself, this is about a year down the line…
.jpeg)
Partners across the value chain and growing the team of scalemakers
We are continuously working with getting ourselves into the textile community as a collaborative partner – for the automotive, fashion/apparel, and home interior segments as well as across the full value chain. We are actively sourcing feedstock in all three major regions in the world, building relations and partnerships around polyester waste. More on this later. Finally, we have added some more amazing talents to our team – with experiences from Eastman, Stena recycling, Dupont, Spinnova, Bestseller, and more. In the end, it is all about the team which will execute the plan. I am convinced this is our biggest asset at Syre.
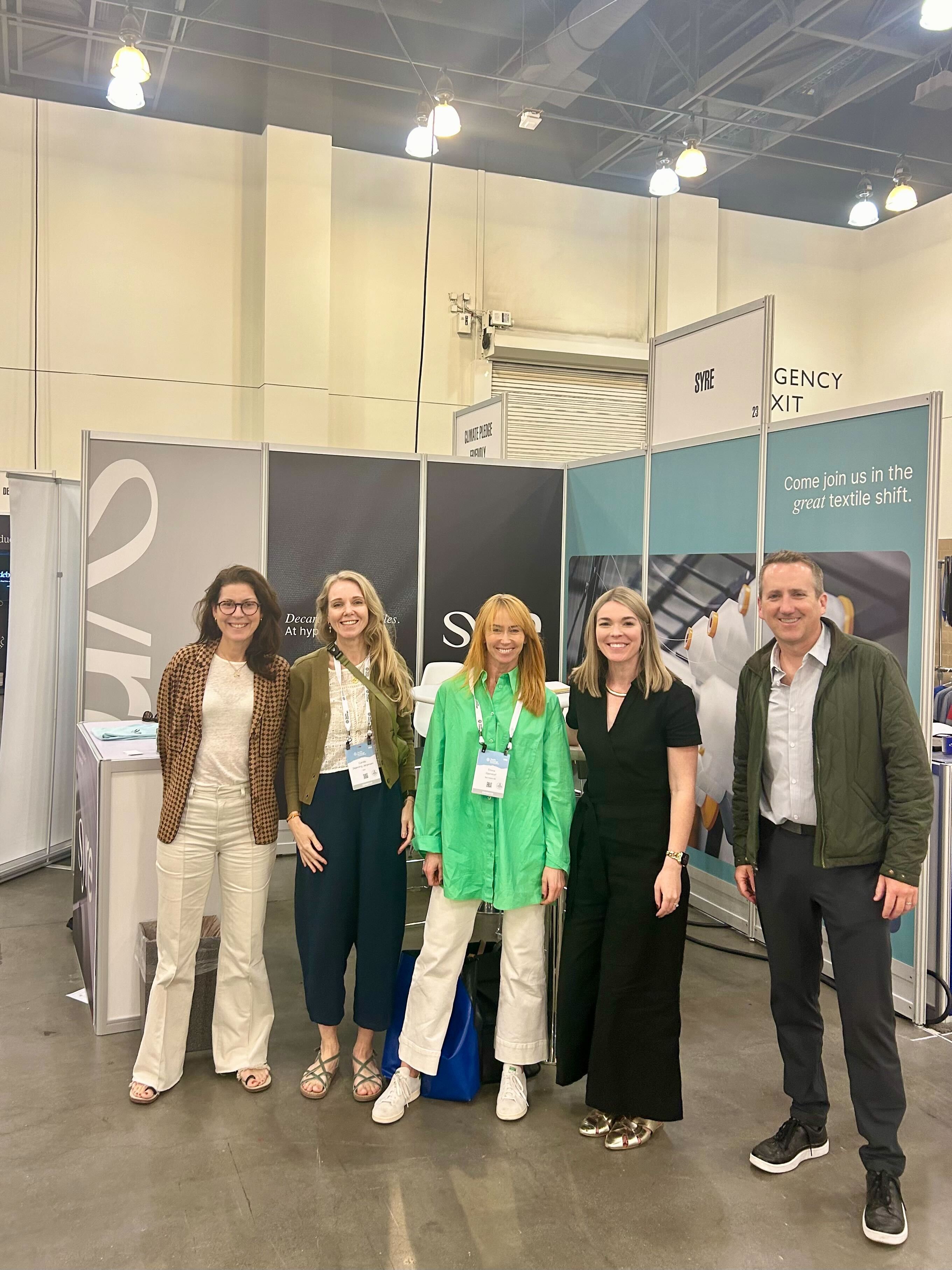
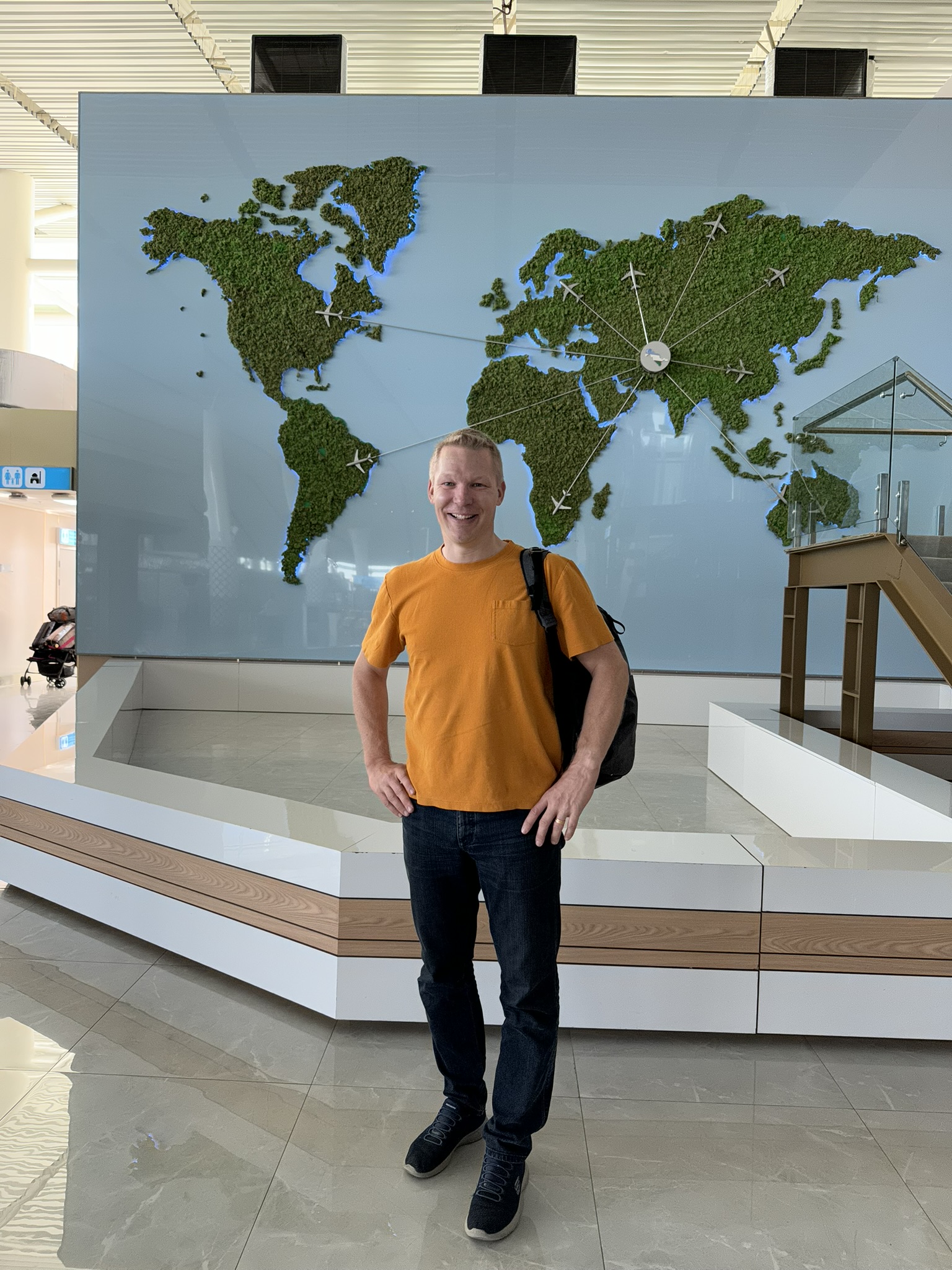