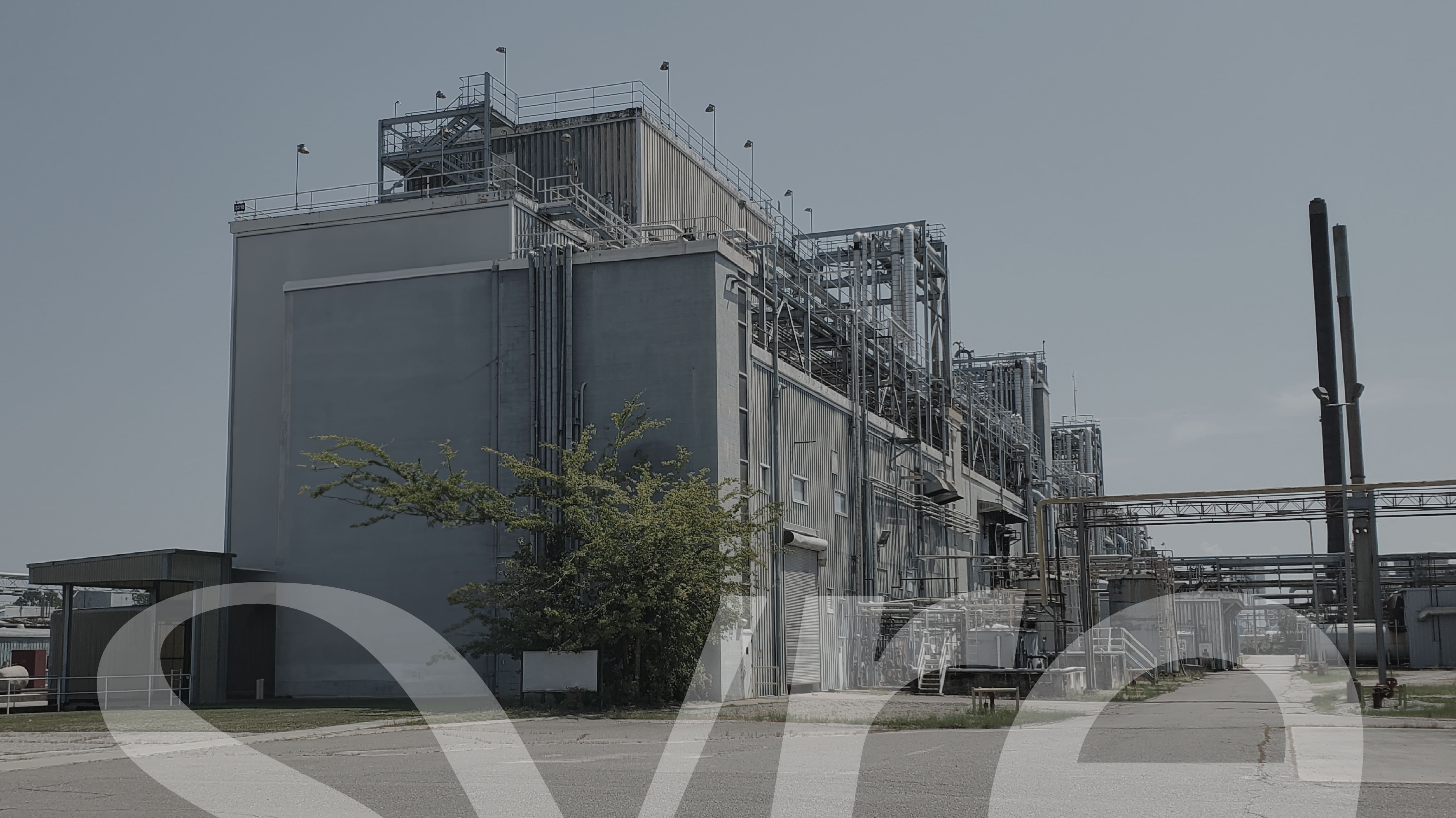
A blueprint for reinventing an industry
The big challenge of the textile industry hasn’t been the lack of innovation or remarkable inventions — it's that these have had a hard time leaving the lab and into scaling for actual impact. This is why Syre was born. By proving that large-scale, textile-to-textile recycling is achievable and at pace, we can begin to transform the industry responsible for up to 10 percent of global CO2e emissions.
Last week, we announced a key milestone on this journey. In Cedar Creek, North Carolina, we have taken the first major step in realizing our plans to reshape the textile industry. With the announcement of our Blueprint plant, we are putting our ambition into action.
Scaling for the future
When operational in mid 2025, the Blueprint plant will be able to produce up to 10,000 metric tons of circular polyester annually, equivalent to approximately 50 million T-shirts. Ready for commercial batches and a notable achievement on its own. However, this is only the beginning. Based on this blueprint, we will rapidly scale our operations to meet the massive globa ldemand for circular polyester, using this facility as a model for our future, much larger plants.
By 2027, we aim to have our first gigascale plant operational, producing up to 250,000 metric tons of circular polyester. By 2032, we plan to have multiple gigascale production plants running at full capacity, collectively producing over 3 million metric tons annually and abating more than 15 million metric tons of CO2e. This plan reflectsan unprecedented speed and scale in the industry, all while tackling thecomplexities of the textile value chain and the regulatory landscapes.
Building success through partnerships
For the Blueprint plant, we formed a strategic partnership with Selenis, a leading global supplier of high-quality specialty polyester solutions. The partnership will see the existing Selenis production plant in Cedar Creek expand as Syre builds an adjoining new plant to form a continuous production flow. The coming together of the two will combine new technologies in depolymerizing and polymerizing for textile-to-textile recycling all in one place, allowing for a cost efficient, industrial scale operation.
“When scouting locations for our plants, we have to carefully balance critical factors such as renewable energy, infrastructure, cost and access to feedstock. I am really excited to partner with the Selenis team, having a similar sustainability direction and ambition to drive green transformation at scale”, says Dennis Nobelius.
How every fiber gets new life
So how does it actually work? In four overall steps, the textiles that enter our Cedar Creek plant are sorted, shredded, broken down into foundational building blocks, and reassembled into circular polyester,with quality on par with virgin polyester – but with a superior sustainability performance.
1) Pre-treatment: Feedstock (i.e. textile waste from post-consumer scrap or production spill) is shredded, metals are separated, and lastly the textile fibers are granulated.
2) Depolymerization: The granulated textile fibers then go into the de-polymerization step, where the polymers are broken down to monomers.
3) Polymerization: In the polymerization step the monomers are restructured into polymers again, moving onto the PET-chips production.
4) Yarn-spinning: Final step will be the yarn spinning process, through key partnerships.
With close proximity to our R&D team and Pilot line in North Carolina, our ambition is that this plant will serve as a hub that integrates research, innovation, and production—and helps accelerate the textile industry's efforts to reducing its carbon footprint by adopting circularity.
A blueprint for the entire industry
We recognize the challenges. Building a large plant, especially one that is the first of its kind, will for sure have its learning curve. For us, we're not just building a factory; we're also writing the manual for our journey to come.
Our Blueprint plant is a practical advancement towards a circular future where every textile fiber sees a new day. As we set out on this path, we do so with humility and determination, ready to learn and continue to move at speed. And we are inviting and encouraging more early movers and industry partners to join us.
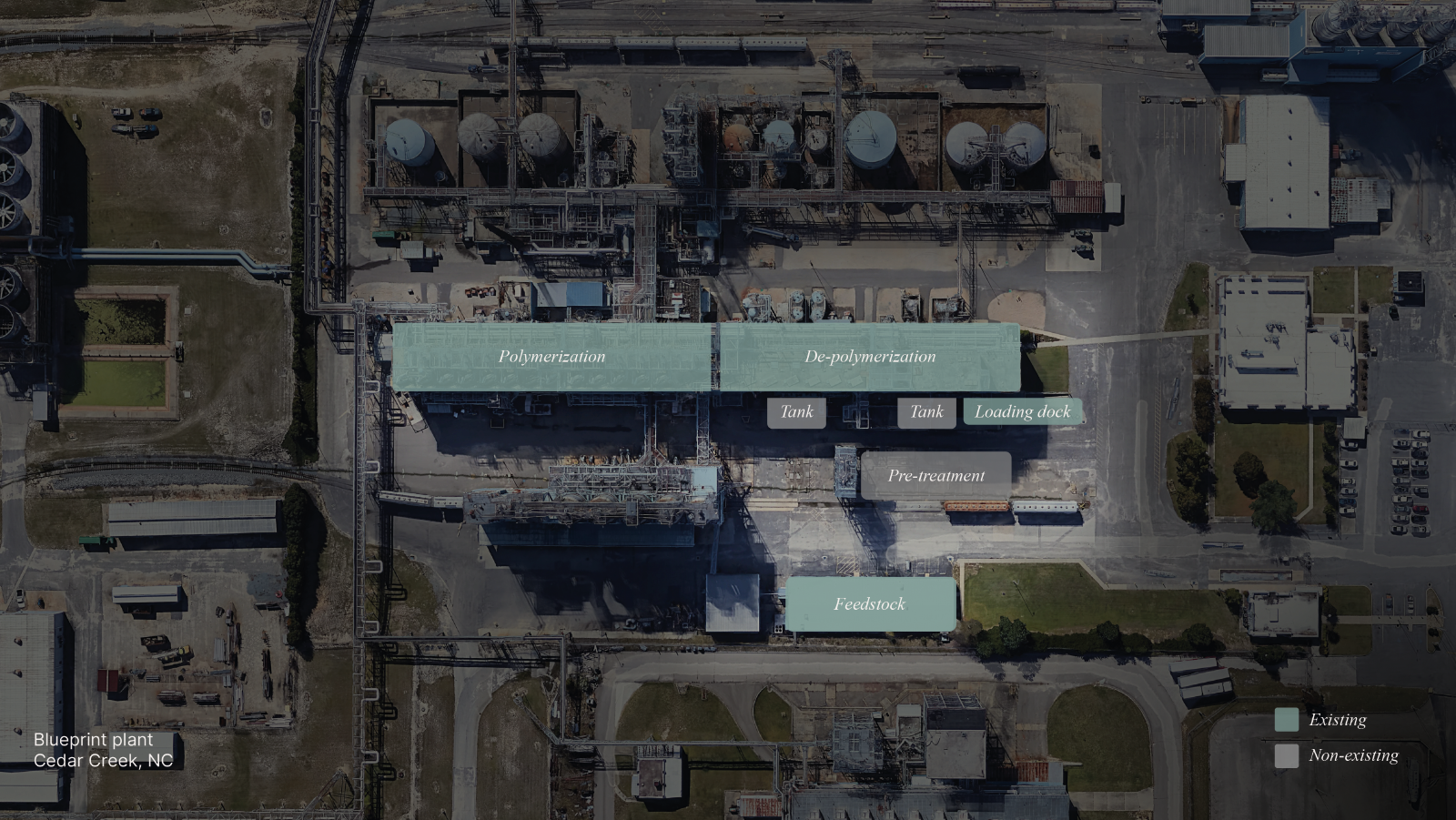